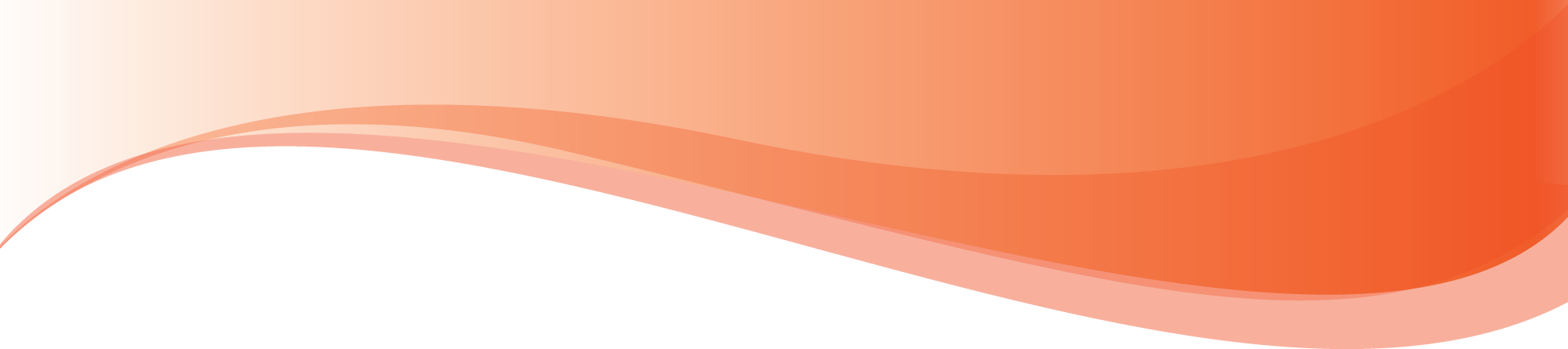
Double Shute or On-edge machine is best suitable for naked products in round, rectangle or square shapes. The double hopper feeding and auto stack selection by the pusher is an advantage and reduces the manpower to a certain limit. The PLC controlled with a touch screen panel makes it user-friendly and is easy to set parameters. The speed can be varied up to 120 packets per minute according to stack length.
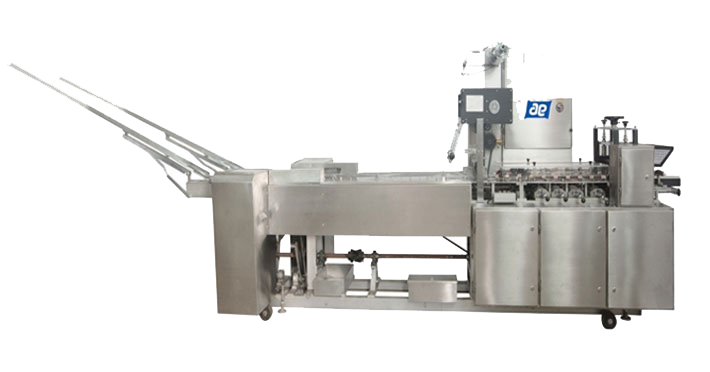
Dimensional Drawings
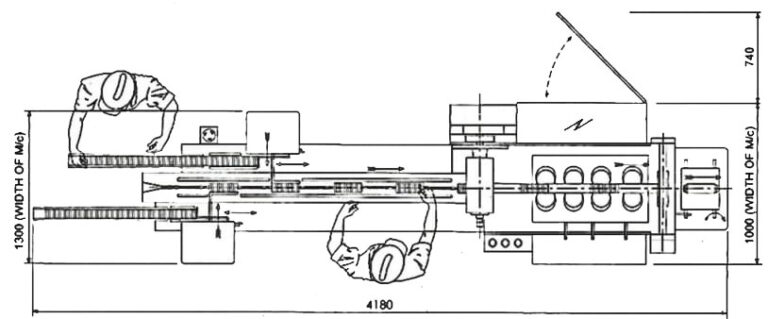
Machine Specifications & Technical parameters
Electrical Data:
Power Supply | 3 Phase, 3.5 KW | 440 V With neutral. | |
Main Motar | 3 phase/1 phase 6 Lead | 2 HP, 1440 rpm, 440 V, 50 Hz | |
Main Drive | 230 V, 2 HP | Input | Output |
Single Phase | 3 Phase | ||
Jaw Heater | 50 V, 350 W – 4 No (Check the actual wattage) | ||
Dish Heater | 50 V, 400 W – 4 No (Check the actual wattage) | ||
Transformer | Primary – 2 Phase, 440 V, Secondary – 50 V, 30 A+ 30 A |
Note:The electrical specifications are subject to change with our different types of models and functions of machines
Technical Parameters & Specifications:
Product Size Range | 40 mm (W) x 20 mm (Ht) x 3 mm (thk) To 60 mm (W) x 60 mm (Ht) x 8 mm (thk) |
Stack Size Range | 50 mm to 200 mm |
Wrapper Size Range | 80 to 250 mm Cutoff Length &100 to 300 mm wrapper width |
Type of Product | Should be stiff or hard and round or rectangle or square in shape. |
Speed | 120 Packets per Minute (PPM) (depending upon the size of the product). |
Feeding | Double hopper feeding with belt conveyor. |
Control | PLC controlled |
Machine Dimension | 4180 (L) x 1300 (W) x 1675 (H) |
Weight | 1000 kg (Approx.) |
Wrapping Material | BOPP laminated, LD Polyester, Heat Sealable Laminates Containing Aluminum Foil. Maximum 12″ Roll diameter. |
Note: The designs/specifications are subject to change without notice on account of continuous improvement in machine quality
Special Features
-
01 PLC controlled with touch screen & password protection for the machine settings.
-
02 Easy to set the different cutoff lengths by putting the desired value in HMI (optional as per model selection) & as well as adjust the jaw dwell position in one stand operation.
-
03 Malfunction display through self-alarm with message.
-
04 AC motor with Variable Frequency Drive.
-
05 Highly sensitive photoelectric scanner to monitor the pouch length and the cutting position. "I-mark position can be adjusted while the machine is running.
-
06 Epoxy liquid painted structure with SS 304 safety guards and electric control panel (optional as per selection).
-
07 Double hopper feeding with belt conveyor and auto stack selection by pusher and loader.
-
08 End cutter and sealer have provision for single& double jaw system for high production.
-
09 Overall durable, compact, practical, low maintenance and affordable. Suitable for working long hours without breakdown and without need of constant supervision.
